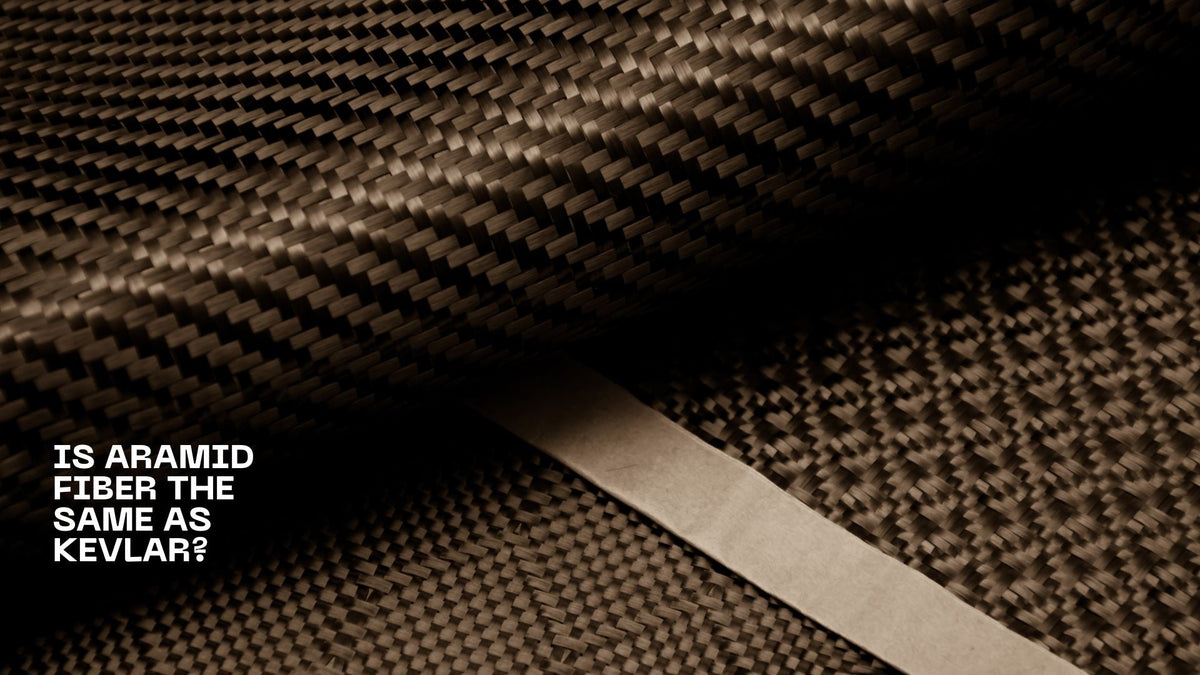
Aramid Fiber vs Kevlar: A Comparison Guide
|
|
Time to read 5 min
|
|
Time to read 5 min
Aramid Fiber and Kevlar are two high-performing materials with incredible heat resistance and strength that are popular in various industries. Although these terms are often used interchangeably, they are not exactly the same.
In this article, we’ll clear the air on some common misconceptions about aramid fiber and Kevlar and explore their applications.
Here is a short, straightforward difference between aramid fiber and Kevlar. Aramid fiber is a type of strong synthetic material inherently resistant to flame and heat. Kevlar, on the other hand, is a popular para-aramid manufactured by a commercial brand, DuPont™.
🔑 Key Takeaways:
Aramid is the general name for the fiber material, while Kevlar is the trade name of its manufacturer, DuPont.
Aramid fiber and Kevlar contain high-performance properties with an incredible strength-to-weight ratio.
Many manufacturing industries, big and small, use aramid fiber for its heat, flame, and cut resistance.
Both materials were first used in protective gears, automotive, and similar settings.
⏳In a Nutshell: According to US Federal Trade Commission standards, an aramid fiber must have at least 85% amide bonds in its chemical structure linked directly to two aromatic rings to be classified as one.
Aramid fiber is a generic term for a family of synthetic fibers celebrated for their high strength-to-weight ratio and excellent heat resistance. These properties stem from their unique molecular structure, which consists of long chains of aromatic polyamide units.
Its mechanical properties are better than steel and glass fibers on equal weight. For this reason, aramid fiber has been widely used in aerospace, automotive, and industrial textiles settings.
For some time now, manufacturers have sought aramid fiber to improve work safety for industrial workers. These include:
Fire-resistant clothing
Heat-resistant gloves
Protective gears
Kevlar is a trademarked brand name for a specific type of para-aramid fiber developed by DuPont™. It has gained iconic status due to its exceptional strength and bulletproof qualities.
Unique properties of Kevlar include its:
High tensile strength
Excellent cut resistance
Remarkable heat tolerance
These attributes, such as body armor and helmets, have made it a preferred choice for ballistic protection.
Key applications of Kevlar extend beyond personal protection and encompass areas like marine cables, brake linings, and even musical instrument strings.
Aramid fiber and Kevlar, while distinct, share fundamental characteristics that contribute to their exceptional performance.
Both materials are composed of long chains of aromatic polyamide units. This molecular structure is the cornerstone of their extraordinary strength and heat resistance, enabling them to withstand temperatures exceeding 500°C.
Aramid fiber and Kevlar are renowned for their exceptional tensile strength and ability to endure extreme heat. These properties are directly linked to their shared chemical makeup, making them invaluable in demanding applications.
Due to their impressive performance profiles, both aramid fiber and Kevlar find applications in industries requiring robust, lightweight, and high-performance materials. Their versatility is evident in everything from aerospace and automotive components to protective gear and industrial textiles.
While aramid fiber is a broad category, Kevlar represents a specific type within that family. This distinction leads to notable differences in their characteristics and production processes.
The methods employed to produce aramid fiber and Kevlar vary, resulting in distinct performance attributes. Kevlar's manufacturing process is meticulously controlled for its exceptional strength and durability.
Due to differences in their production and molecular structures, aramid fiber and Kevlar exhibit varying performance characteristics. While both offer impressive strength and heat resistance, Kevlar generally excels in these areas, making it the preferred choice for applications demanding maximum protection.
Kevlar's superior performance often comes at a premium. Kevlar tends to be more expensive than other types of aramid fiber due to the specialized manufacturing processes and research invested in its development.
✅ Pro Tip: Physically, you can distinguish between aramid fiber and Kevlar by looking at their color. Kevlar is a brighter yellow, and normal aramid fiber is a darker yellow. Darker yellow usually means the fiber has been exposed to UV or sunlight, which is bad for Kevlar. For the best quality, opt for a pure yellow color.
The versatility of aramid fiber and Kevlar is evident in their widespread applications. From the bulletproof vests worn by law enforcement and the protective gear used by firefighters to the automotive industry reinforcing tires and body components.
This increasing need for protection is why phone case industries like Thinborne created an aramid fiber phone case. It incorporates aramid fiber and Kevlar for its protective qualities while maintaining a sleek design. These cases offer a balance of durability and aesthetics, appealing to tech-savvy consumers like Shane Craig.
Here's his review of Thinborne's Galaxy Z Fold 6 thin aramid fiber case, the latest Samsung foldable phone:
🛒 Buyer Tip:
Aramid fiber and Kevlar are indeed closely related, but they are not identical. Aramid fiber represents a broader category of synthetic fibers, while Kevlar is a specific type with exceptional properties. Understanding the nuances between these two high-performance materials is crucial for making informed decisions in various industries.
Knowledge of aramid fiber and Kevlar helps manufacturers choose the best type for personal protection, industrial use, or technological advancements.
Generally, Kevlar is considered stronger than other types of aramid fiber due to its specific manufacturing process and molecular structure. However, the strength can vary depending on the specific type of aramid fiber and its intended application.
Aramid fiber vs carbon fiber are both high-performance materials, but they have distinct properties. Aramid fiber excels in heat resistance, flame resistance, and impact resistance, while carbon fiber is renowned for its high strength-to-weight ratio and stiffness.
Aramid fiber itself is not waterproof, but it can be treated or combined with other materials to create water-resistant or waterproof products.
Aramid fiber is recyclable but challenging due to its complex chemical structure. Research and development efforts are ongoing to explore potential recycling methods.